Factory Visit: Industry Nine, Asheville, North Carolina
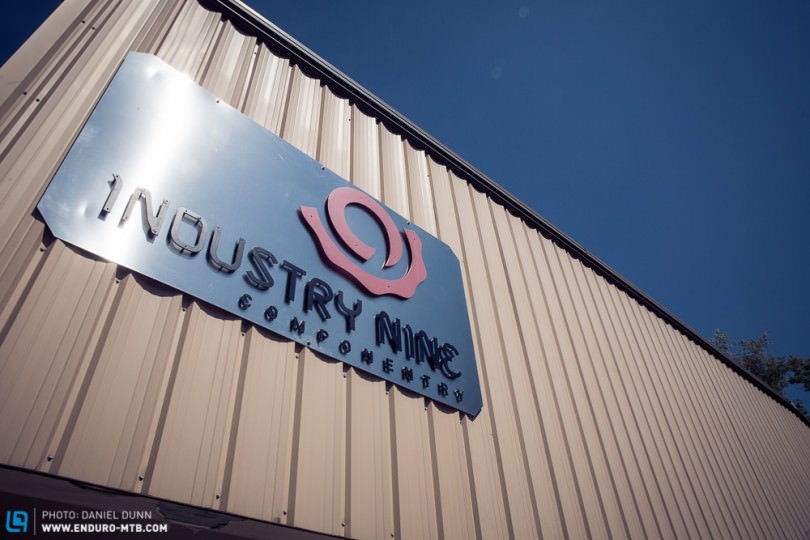
After visiting with Industry Nine owner and head engineer Clint Spiegel for a few minutes, a few things became clear. His passion for high quality in the design and manufacturing of his products. And the overall passion of employees at I-9 for putting together some pretty kick ass wheelsets.
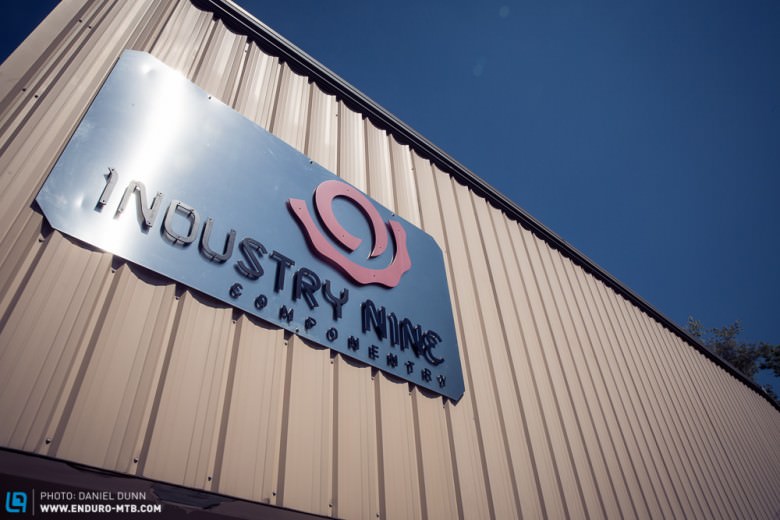
About 20 years ago, Spiegel was exposed to the bicycle component manufacturing industry while machining parts for early Rock Shox models, when those forks were put together in the building that is now Cane Creek, back then was Dia-Compe. He also worked with some engineers at Cane Creek on hub designs that ultimately never went anywhere.
As years went by, and his own passion for riding mountain bikes grew, he re-investigated ideas on hub and drivetrain design, and realized it was time to start his own company. Industry Nine was born.
We talked a bit about manufacturing in the USA, and competing with the onslaught of parts built in Asia. “We believe in making stuff as locally as we can, and employing people in this country, rather than outsourcing everything, so part of it’s a philosophy. But also when you have an idea, and the manufacturing capabilities on hand, you’re able to realize the idea quicker and then modify and tweak it and redevelop it a lot faster than say, if you were on a computer creating a design and then sending it to Asia and waiting many, many months for it to come back. But it also gives us a lot more control with our processes, our quality can be higher, and it also allows us to be a lot more custom. We are able to offer a lot more variations in the builds, we’re able to adapt to new industry standards, like axle configurations, very, very quickly and bring them to market and be more responsive to our customers.”
“We try to take a philosophy of no compromise, using the best material, the best processes, the secondary processes that increase the longevity. Everything we do, we try to maximize that quality.”
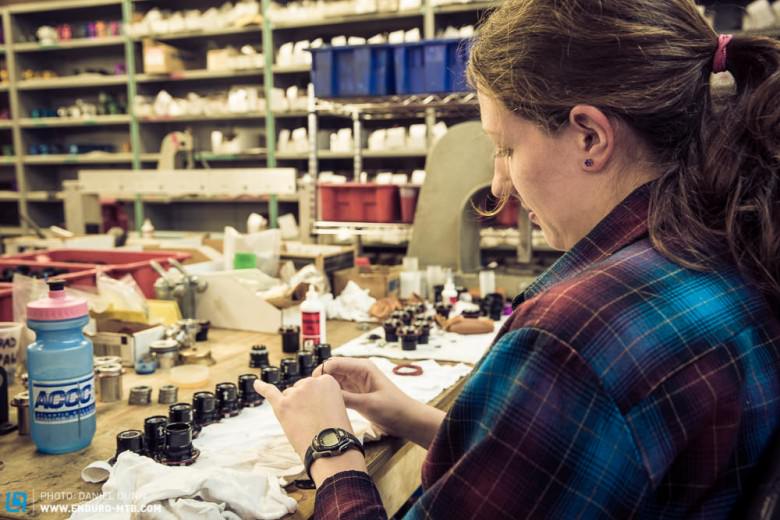
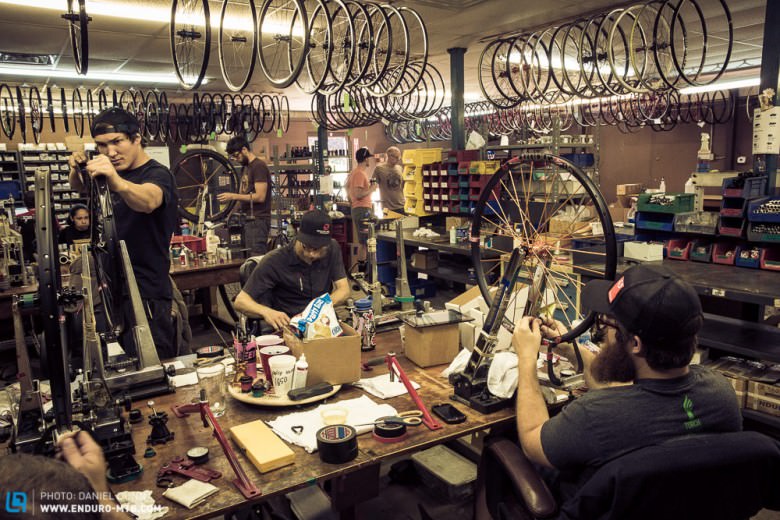
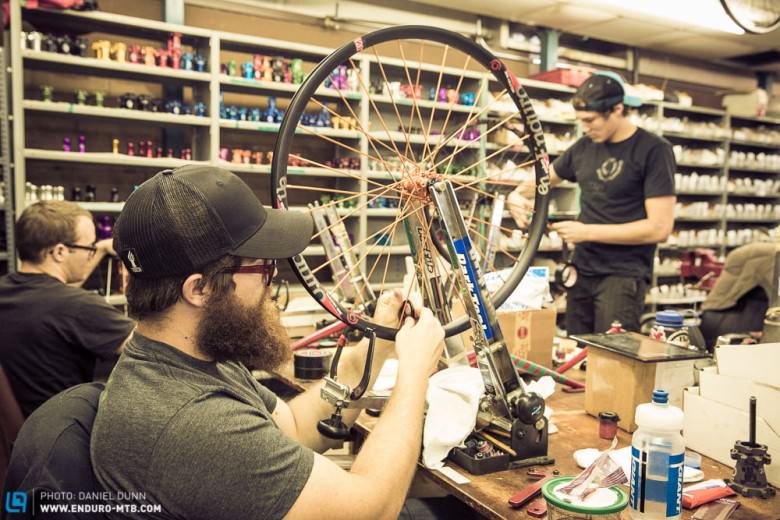
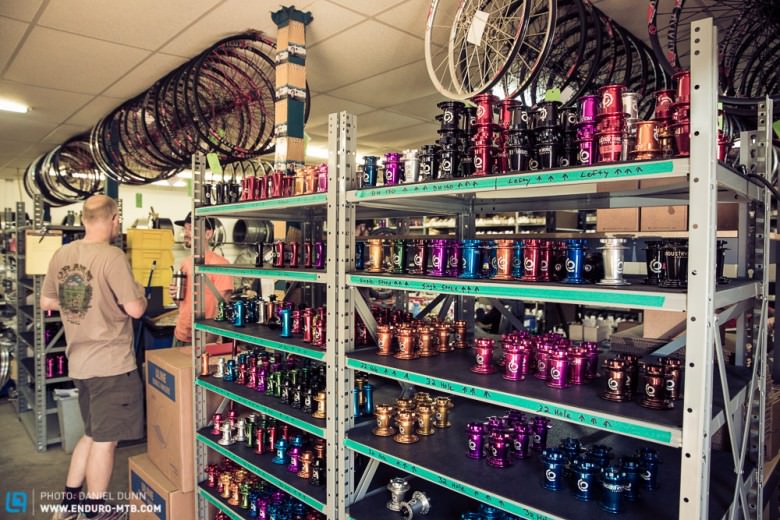
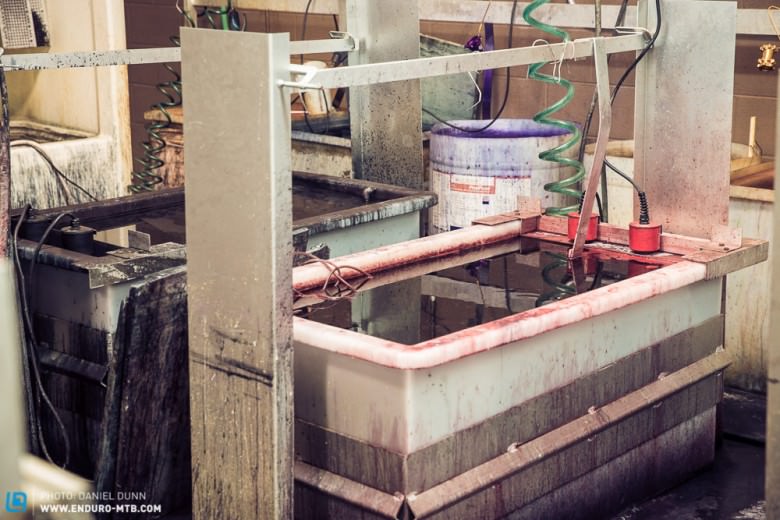
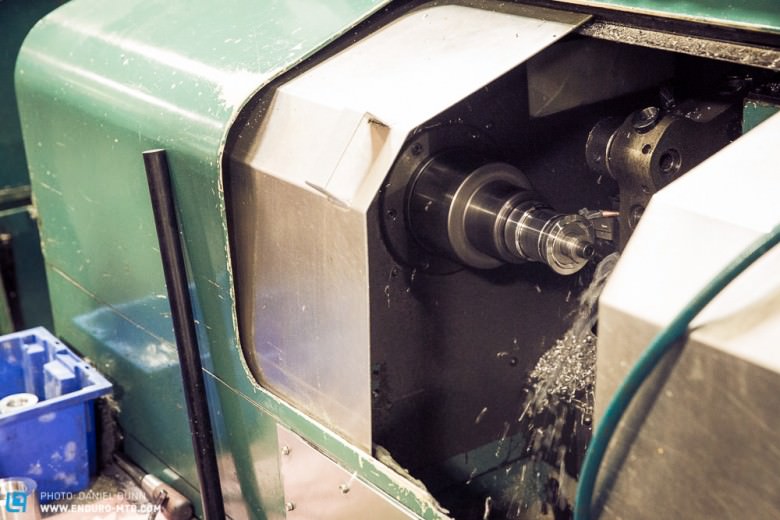
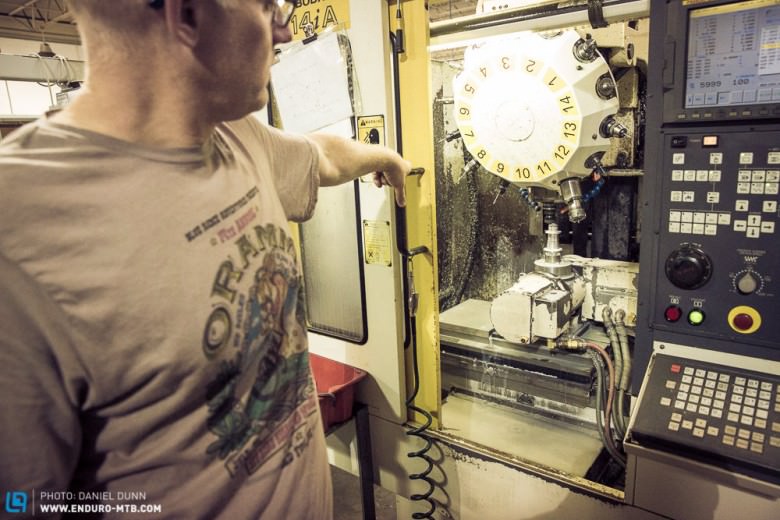
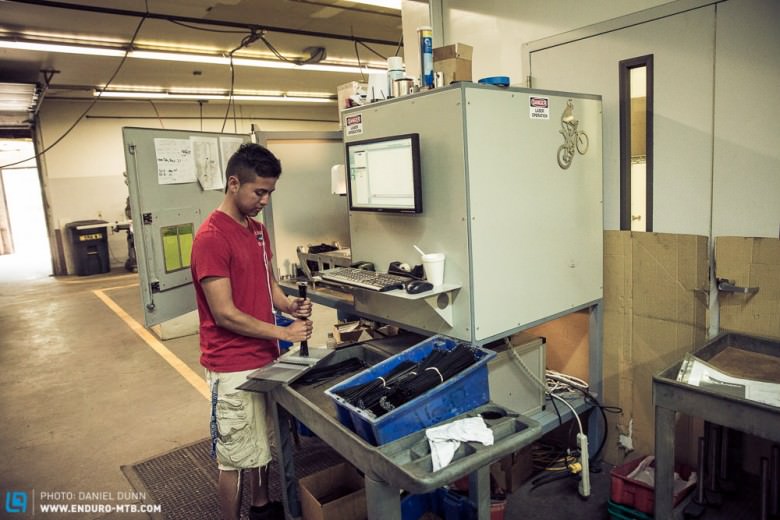
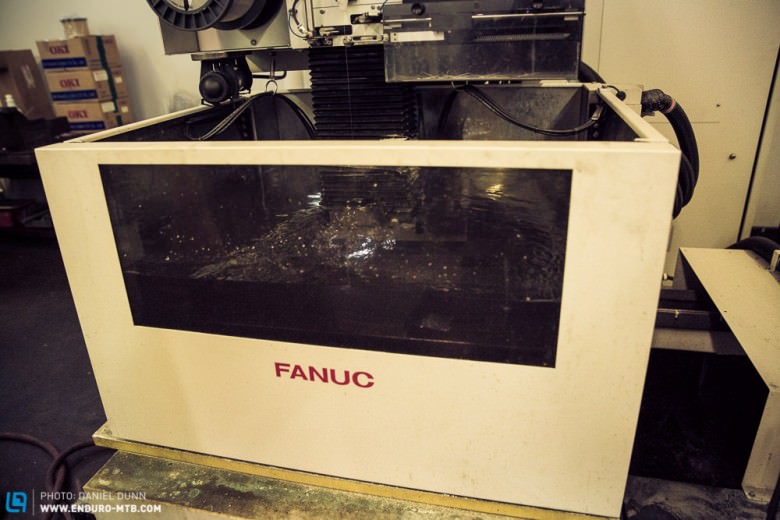
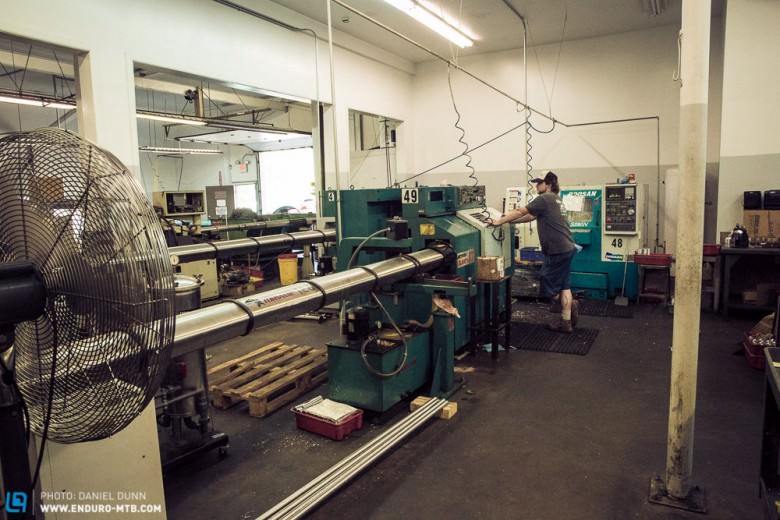
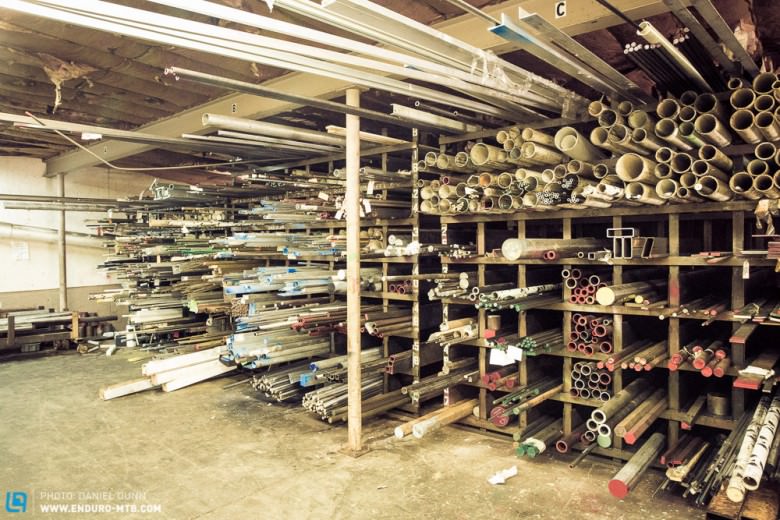
Moving onto the subject of the amazing riding in the Asheville area and how that benefits I-9. “Obviously, being where we are, any of our designs have a great test bed, a great group of riders to test it. When we’re bringing out a new product, between the riders here, the people we know, and our buddies are ready to ride it immediately, and really put it through some abuse.”
“It works out great for people who have moved to this area for the amazing riding. We find them, and those hard core riders are working here, which brings a lot of passion to the company, a lot of energy, a lot of new ideas. It works out great. I think this is a unique area that really helps this company thrive.”
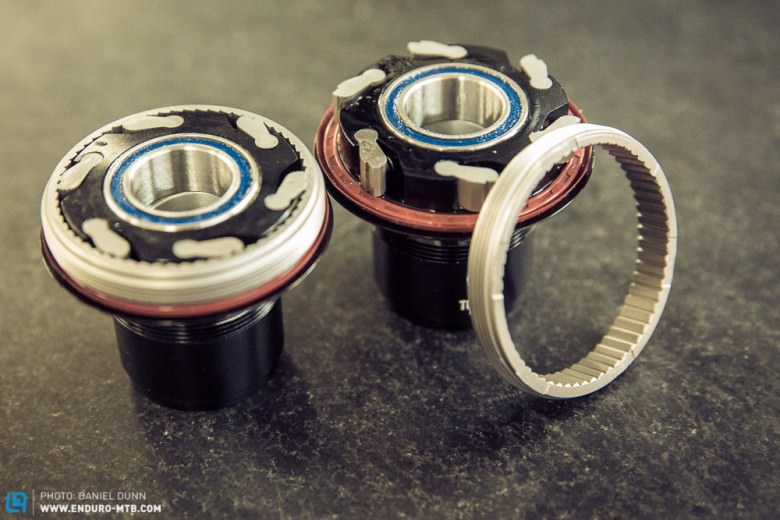
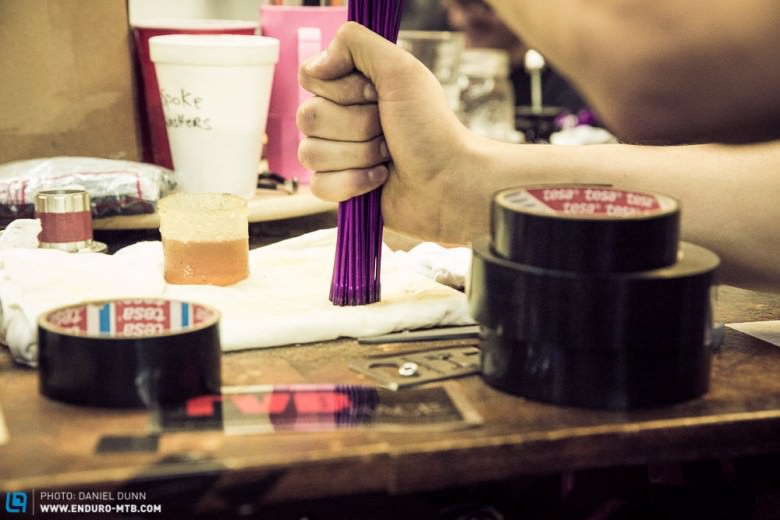
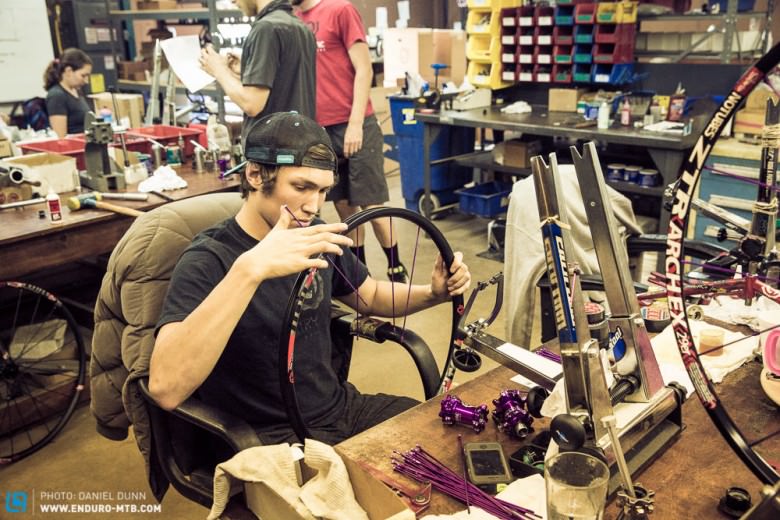
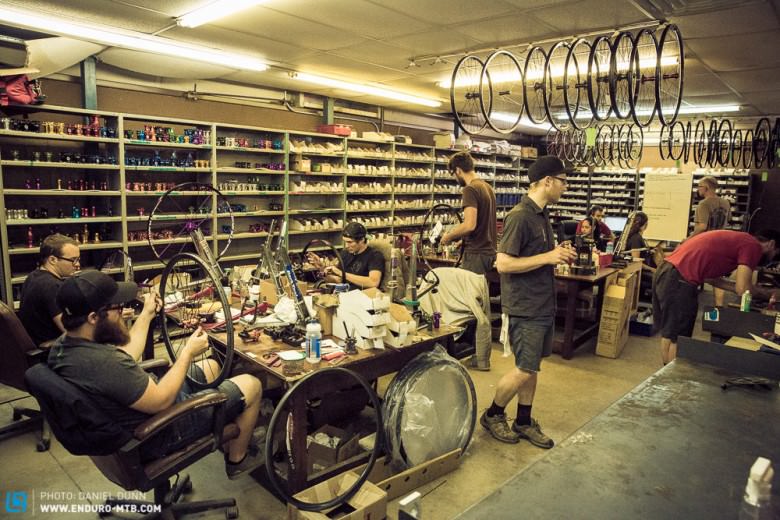
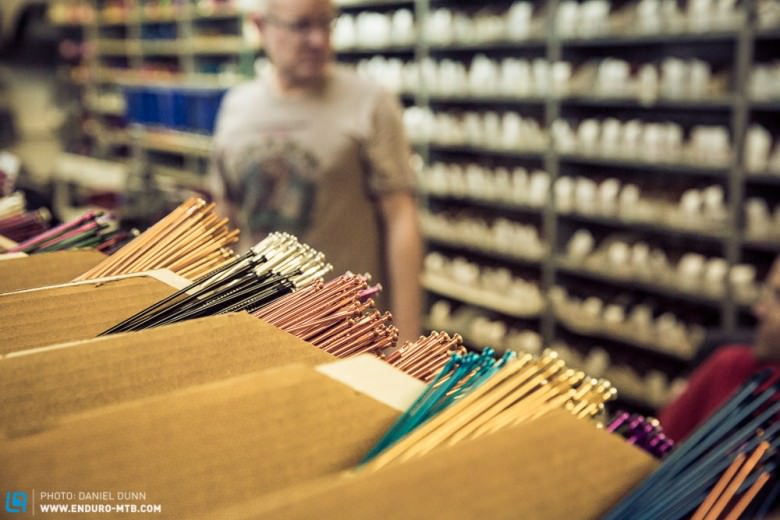
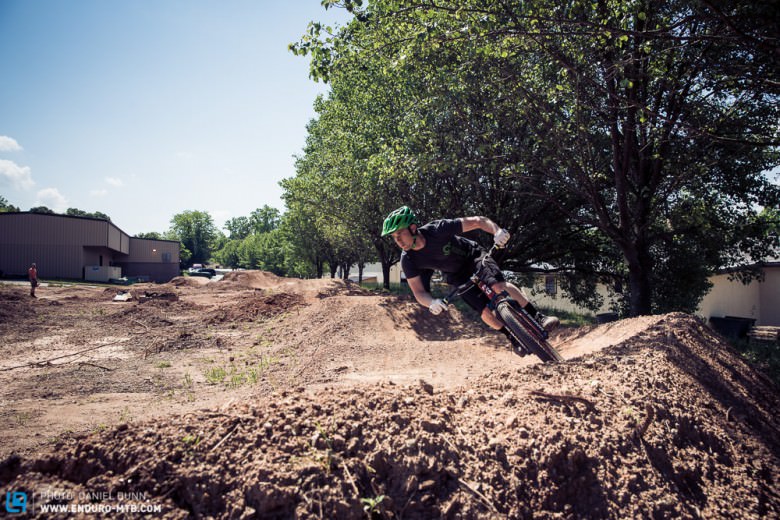
One thing that sets I-9 apart from other companies is Spiegel’s experience basically growing up in a machine shop. Not only does he know all the various CNC machines inside and out, but he knows how to create a radical design manufacturable. Sometimes, amazing designs will sit on the table for years, because they’re simply cost prohibitive to bring to real life. Spiegel’s designs come from a huge pool of experience in multiple worlds. The bike design world, and what works really well for the job it’s needed to do, but also what can be produced, at a high quality, at a cost that’s beneficial to remaining in business, but also reachable for conscious customers. “Form follows function. I’m very much into making it beautiful, but, it’s gotta be beautiful based on the function it’s performing. It absolutely has to follow the function of the part.”
Where does I-9 go from here? They’re growing, does it continue? “As long as we stay creative, and pay attention to detail and quality, I think we’ll keep growing, and hopefully, strongly.”
Words, Photos: Daniel Dunn
Did you enjoy this article? If so, we would be stoked if you decide to support us with a monthly contribution. By becoming a supporter of ENDURO, you will help secure a sustainable future for high-quality mountain bike journalism. Click here to learn more.